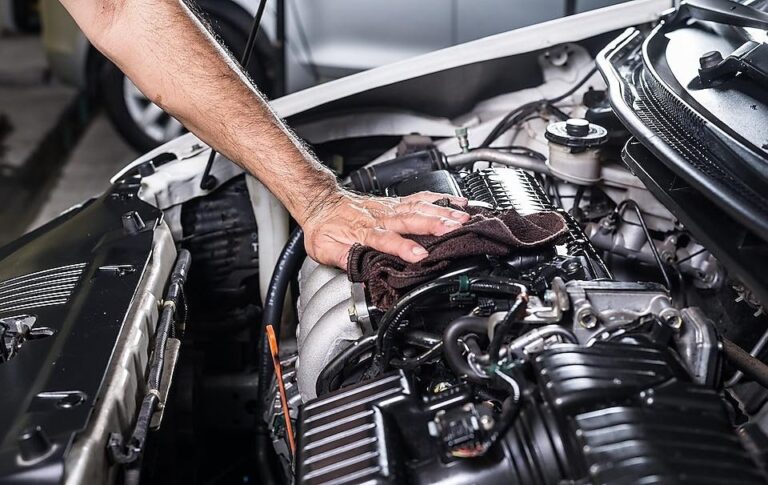
Every year a large number of dollars are spent for new plant hardware intended to construct things better and quicker. Be that as it may, machines continue to separate.
Bearing disappointment is a noteworthy reason for hardware vacation in the present industrial condition, regularly resulting from ill-advised grease. Ill-advised oil situations include the contamination of the ointment by residue, soil and dampness, inadequate measures of grease connected to the bearing, as well as over lubrication of the bearing.
Each bearing disappointment legitimately impacts the generation cycle. While bearings can be costly, substitution cost alone is regularly miniscule contrasted with lost creation and the expense to fix the harm.
Why, in the period of innovation, is this an issue? It is on the grounds that numerous bearings are as yet greased up physically. Regardless of how constantly a maintenance staff clings to an oil plan, it is a troublesome assignment. Since representatives are required to deal with different duties in the lean condition of the present plants, usually legitimate oil isn’t viewed as a need.
Advantages of Automated Lubrication
Each bearing, paying little heed to size or area, should be greased up appropriately. Inappropriate oil will result in high, yet superfluous expenses for the activity. A portion of the immediate expenses resulting from inappropriate oil include substitution bearings, work for substitutions and fix, overabundance ointment and work for inefficient manual practice. A portion of the indirect, yet genuine expenses are vacation or lost creation; item spoilage because of overabundance ointment; natural, wellbeing or housekeeping issues; and abundance vitality utilization.
While oil weapons and manual oil appear to take care of business for some maintenance activities, their advantages frequently can’t measure up to those given by a mechanized oil framework as far as efficiency, ecological issues and specialist wellbeing. A robotized oil framework avoids bearing disappointment by providing the perfect measure of the right (new, clean) oil at the opportune time to the ideal spot.
The main distinction among robotized and manual grease is that for the situation of physically connected lubricant supplier in Dubai will in general grease up on timetable (when daily, week, month, year, and so on.) as opposed to when the bearing needs it. To redress, the administrator regularly will fill the bearing until he sees ointment seeping out. The ointment could be adequately “spent” when the administrator hits it up again. This sets up an over lubrication and under lubrication situation. On the other hand, robotized oil gives oil continually at a suitable sum that enables the bearing to work at its ideal. At the point when the bearing is appropriately greased up as such, it additionally seals the bearing from contaminants.
Maintaining legitimate grease on generation hardware diminishes the quantity of breakdowns because of bearing disappointment. Likewise, there is less vacation because of the manual oil process, just as significantly diminished worker hours required for the errand.
Computerized Lubrication System Options
When the choice to computerize oil procedures is made, there are a few choices from which to pick. Accessible frameworks include: single-line parallel, two-line parallel, single-line dynamic, fog grease, minute-volume/low-weight shower, recirculating oil, siphon to-point (box) lubricators, single-line obstruction and single-point lubricators. A concise portrayal of each pursues.
Single-line parallel.
This framework is anything but difficult to configuration, install, maintain, change or grow. It commonly works at high liquid weights and can be utilized with oil or oil. In this framework (Figure 3), the siphon pressurizes the main supply line, and a cylinder inside the prepared injector (Figure 4) dislodges a premeasured measure of grease through the outlet to the bearing. The siphon turns off and the supply line weight is vented back to the repository. The spring-stacked cylinder comes back to rest and the release chamber loads up with a deliberate charge of ointment for the following cycle.
Favorable circumstances:
• Easy to plan
• Easy, financially savvy installation
• Individually customizable injectors
• Proven, trustworthy plan
Inconveniences:
• May not be appropriate for combinations of overwhelming lubricants, freezing temperatures, long supply line keeps running among siphon and injectors
Two-line parallel.
This framework is perfect for long pumping separations and outrageous temperatures (Figure 5). It is anything but difficult to change in accordance with meet explicit bearing prerequisites. It gives high weight, up to 5,000 psi, and is intended to work with numerous oil points over a wide region. This present framework’s siphon pressurizes metering gadgets through one side of a four-way, two-position reversing valve (Figure 6) and the principal supply line. The metering gadget control cylinder moves and guides pressurized grease to the main cylinder, which uproots ointment to the bearing. Oil on the opposite side of the control cylinder is vented back to the store during that time supply line and the opposite side of the reversing valve. The reversing valve shifts and the siphon pressurizes the subsequent supply line, repeating the cycle backward.
Favorable circumstances:
• Easily handles thick (overwhelming) oils
• Can oblige long supply line keeps running among siphon and metering gadgets
Hindrances:
• May not be most financially savvy for littler frameworks
• Requires two supply lines (another expense)
Single-line dynamic.
This practical and adaptable alternative is a framework that can be utilized with low-weight oil, oil or high-weight oil. The most recent plans include a preassembled siphon, controller and mono-square cylinder metering gadget. The siphon of this kind of framework gives a deliberate single shot, beat or a continuous volume during the grease cycle. The first prepared cylinder in the square moves, displacing oil to the bearing and diverting stream to the following cylinder. The subsequent cylinder moves and occupies stream to the third. The grouping continues through the metering gadget until the clock or input switch stops the siphon.
Favorable circumstances:
• Accommodates a wide scope of framework control/monitoring alternatives
• Can recognize blockage by monitoring a single point
Detriments:
• One blockage can incapacitate the whole framework
• Large frameworks may require complex piping/tubing runs
Fog grease.
Another straightforward framework, fog oil encourages low oil utilization and cool running bearings. Fog is produced with warmth as well as air flows and is helped through pipe to the oil point with low-weight air. At that point it is measured to the suitable bead before it is administered to the bearing. Shut circle frameworks are ecologically inviting in light of the fact that they return the fog to the generator.
Points of interest:
• Cools and greases up bearings
• Low weight keeps pipe material expense down
• Positive weight helps keep contaminants out of bearings
Weaknesses:
• Environmental/well being worries of “stray fog,” particularly with non closed circle frameworks
• Oil as it were
• Sensitivity to stream, consistency, weight factors
• Extra pipe cost for shut circle frameworks
Minute-volume/low-weight shower.
This framework applies the exact measure of oil required by the lube point and has extremely low oil utilization, as much as 90 percent not exactly different strategies. Ecologically amicable, this framework is perfect for chain grease as it enters the wear points without over lubrication. At the point when the clock flag the beginning of the oil occasion, the injector begins cycling, feeding oil at a controlled rate through little width tubing to the splash spout. All the while, managed low-weight air is coordinated to the spout that blends oil and air to create a fine, controlled, non misting shower.
Points of interest:
• Precise ointment volume and application control
• No “stray fog” issues
• Fast, efficient installation
• Very low ointment utilization
Burdens:
• Oil as it were
Recirculating oil.
This framework is utilized to grease up rolling component bearings and to maintain right bearing temperature. It includes an engine driven siphon that gives a continuous supply of oil through a filtration and piping framework to stream meters. The stream meters control the measure of oil entering the bearing. The oil leaves the bearing and comes back to the supply through another piping framework and return channel. Warmth exchangers or potentially radiators are utilized to maintain right oil temperature. These frameworks are basic on enormous, intensely stacked bearings in procedure industries.
Points of interest:
• Provides both grease and temperature control
• Conditions, expands life of oil
Impediments:
• Most are real, capital installations
• Some advancements require visit manual change at each stream meter
Siphon to-point lubricator.
Handles various oil points independently and is perfect for remote areas This framework, which can beat high back weights, includes an individual, flexible lubricator siphon for each point. Siphon to-point lubricators utilize an electric engine or machine power take-off to pivot a cam running through the drive box/repository. The cam impels individual siphon plungers through a rocker instrument. A plunger at that point draws oil through a needle valve and sight glass and administers the deliberate volume however a high-weight cylinder to the oil point. It is usually utilized on enormous blowers and stationary gas engines.
Favorable circumstances:
• Overcome amazingly high back pressures
• Simple, rough plan
Inconveniences:
• Limited number of grease points
• Relatively staggering expense per point
Single-line resistance.
A simple and cost-efficient system. Designed for closely clustered bearings, this system offers a variety of flow resistance metering devices and can utilize manual, electric or pneumatic pumps. The pump supplies a fixed volume of oil to the metering device through low-pressure tubing. The level of resistance in the metering device determines the proportion of oil flow to each lubrication point.
Advantages:
• Simplicity
• Low price
Disadvantages:
• Oil only
• Reliance on resistance rather than piston metering devices can lead to no positive distribution of oil
Single-point lubricator.
This is a simple and cost-efficient solution for individual, remote bearings. A completely self-contained unit, the single point lubricator is installed at each lubrication point. Gas pressure, spring or electromechanical power delivers the lubricants in UAE over time to the bearing. The reservoir or the entire unit is replaced when the lubricant is consumed, depending on the lubricator style.
Advantages:
• Low purchase price
• Easy to install
Disadvantages:
• Temperature will affect the volume output/service life of many single point lubricators
• Replacement cost rapidly exceeds cost of fully automatic, central systems if the number of lube points increase